Introduction to IPC-A-600
IPC-A-600, also known as the Acceptability of Printed Boards standard. It is a widely recognized industry standard for evaluating the visual quality of electronic assemblies. The standard was developed by the Association of Connecting Electronics Industries (IPC). It is a global trade association representing the electronics industry.
IPC-A-600 provides criteria and guidelines for inspecting and accepting the quality of printed circuit boards (PCBs) and other types of electronic assemblies, such as wire harnesses and cables. The standard covers a wide range of parameters, including conductor spacing, plating thickness, hole size, solder joint appearance, surface finish, cleanliness, and physical damage.
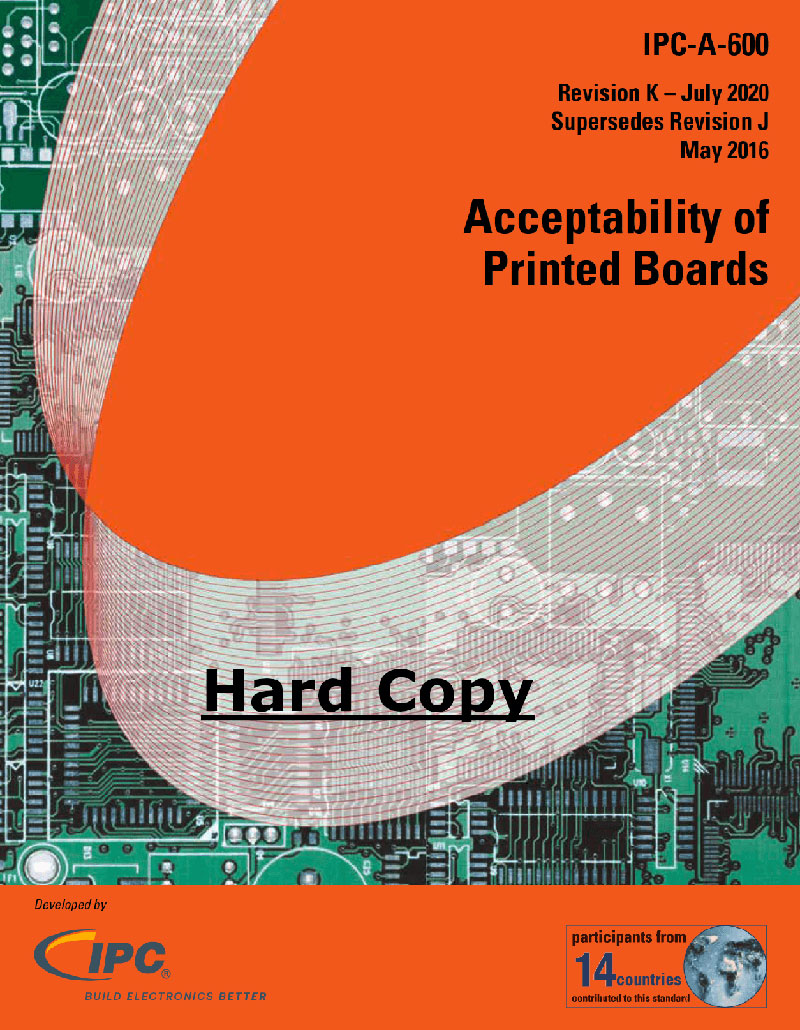
IPC-A-600 defines three classes of electronic assemblies: Class 1 (general electronic products), Class 2 (dedicated service electronic products), and Class 3 (high-performance electronic products). Each class has different requirements and acceptance criteria based on the intended use and expected level of performance of the electronic assembly.
The standard is widely used in the electronics industry as a reference for assessing the quality of electronic assemblies. Compliance with IPC-A-600 is often a requirement in contracts between manufacturers and customers, ensuring that the electronic assemblies meet the agreed-upon quality standards.
IPC offers training and certification programs for individuals and companies seeking to improve their knowledge and compliance with IPC-A-600. By following the guidelines, manufacturers can ensure that their electronic assemblies meet the highest quality standards. And products are free from defects that could impact performance or reliability.
Key Requirements of IPC-A-600
IPC-A600 is a well-known standard used to assess the visual quality of electronic assemblies including printed circuit boards (PCBs). It offers guidance on inspecting and approving the quality of these electronic parts based on their appearance, construction, and performance.
- Conductor Spacing: To prevent short circuits and ensure the proper function of the electronic assembly. When spacing conductors on the PCB, one must meet specific requirements.
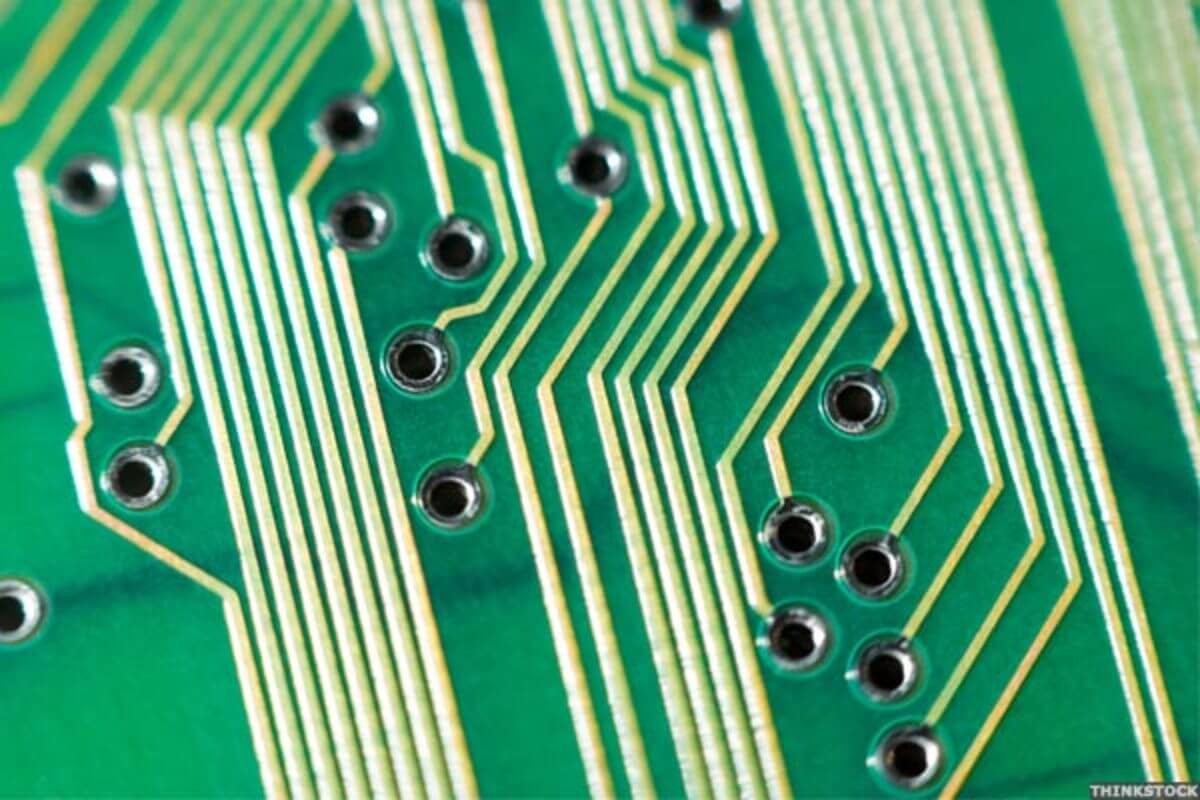
- Plating Thickness: The thickness of the conductors and other metal features on the PCB must meet precise requirements.
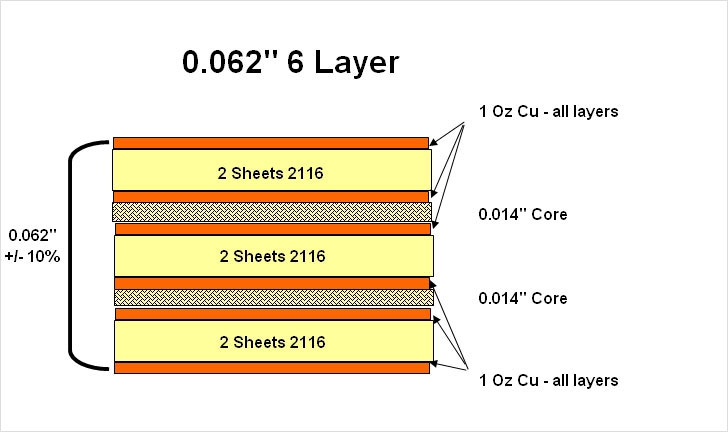
- Hole Size: The holes drilled on the PCB for components, connectors, and vias must comply with specific requirements. It is to ensure they fit and function correctly.
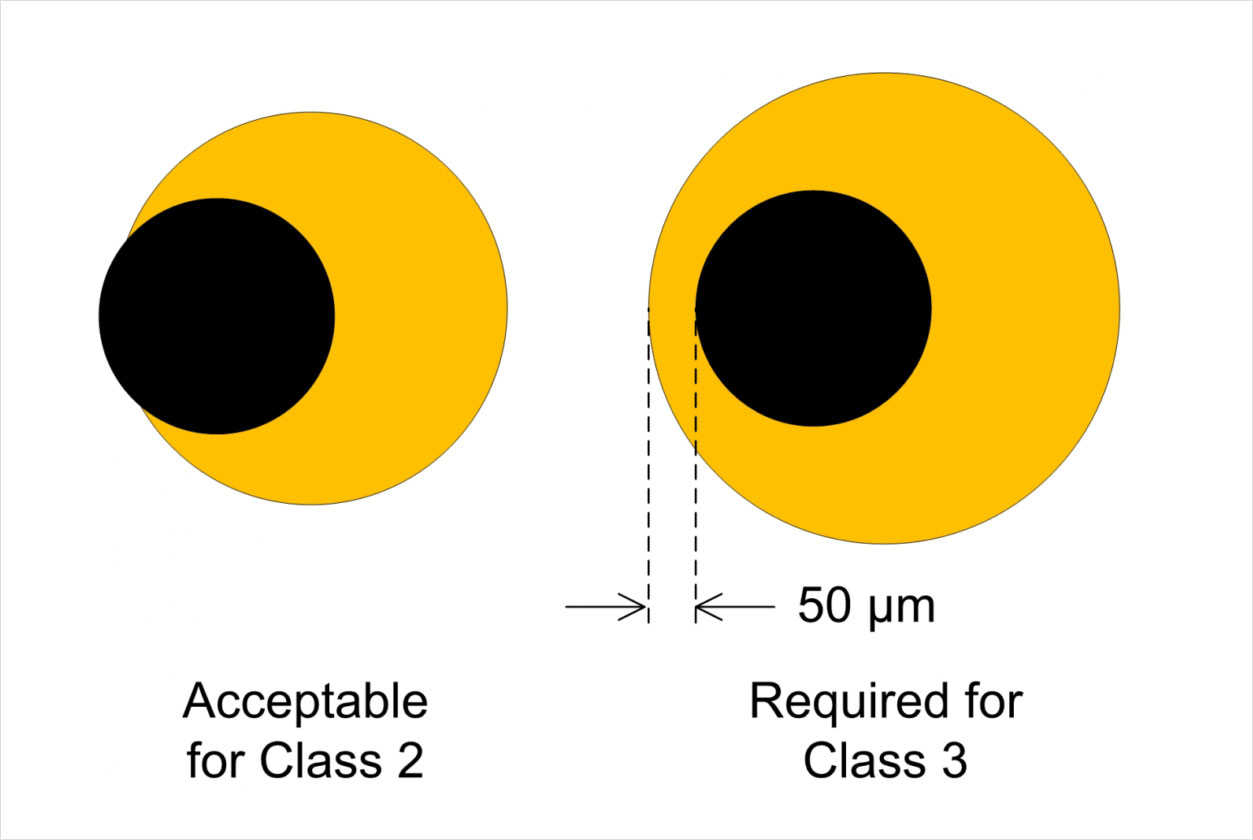
- Solder Joint Appearance: The solder joints on the PCB should meet certain standards. As an example, sufficient wetting, appropriate fillet height, and correct alignment.
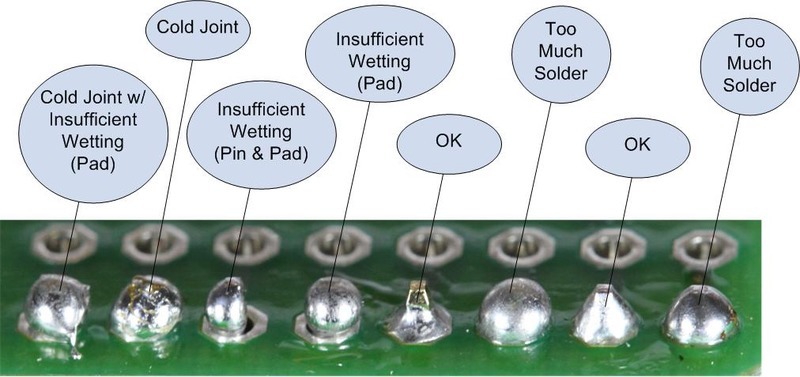
- Surface Finish: For the PCB to have proper electrical conductivity and avoid oxidation, its surface finish should meet specific requirements.
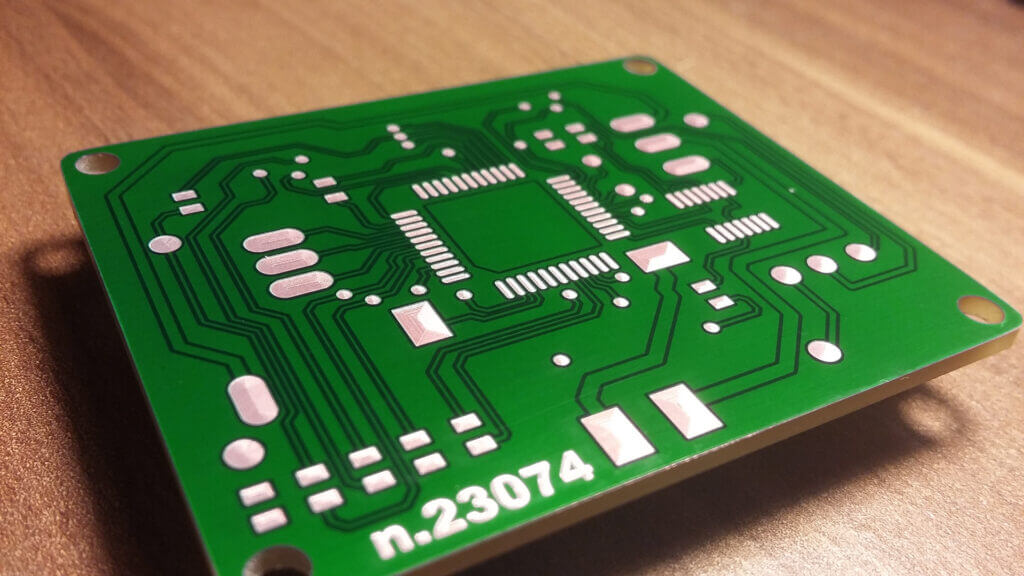
- Cleanliness: The cleanliness of the PCB and other electronic assemblies must meet specific requirements. It is to prevent contamination and ensure proper functioning.
- Physical Damage: The PCB and other electronic assemblies must be free from physical damage. Such as cracks, breaks, or warping, that could impact performance or reliability.
The IPC-A-600 sets the standards for electronic assemblies for their class, which can be Class 1, 2, or 3. Adhering to these guidelines can guarantee that electronic assemblies are of the highest quality and free from defects.
IPC-A-600 Classifications
The IPC-A-600 categorizes electronic assemblies into three classes: Class 1, Class 2, and Class 3. Each class has specific requirements and acceptance criteria that depend on the intended use and expected performance level. Below is a summary of each class.
- Class 1: General Electronic Products -Class 1 assemblies are meant for general consumer or commercial use. Moreover, they are not designed for critical performance, harsh environments, extended use, or wear and tear. The acceptance criteria for Class 1 assemblies are the lowest among the three classes.
- Class 2: Class 2 assemblies for dedicated service electronic products are intended for extended use and harsh environmental conditions. Specially which demand high performance and extended lifespan. The acceptance criteria for Class 2 assemblies are more stringent compared to Class 1.
- Class 3: High-Performance Electronic Products - Class 3 assemblies are designed for high-reliability applications. Mainly where the failure of the electronic assembly could result in significant damage to the equipment or end-user. These products are expected to function during extreme environmental conditions. Acceptance criteria for Class 3 assemblies are the highest of the three classes.
The IPC-A-600 standard outlines different requirements. They are conductor spacing, plating thickness, hole size, soldering appearance, surface finish, cleanliness, and physical damage. The acceptable levels for each criterion also vary based on the class of the assembly. Adhering to these guidelines and criteria helps manufacturers maintain high-quality electronic assemblies that are suitable for their intended purpose.
Common Defects in PCBs and Electronic Assemblies
Defects can impact the performance and reliability of PCBs and electronic assemblies. The following are some common defects that may occur.
- Solder bridging: This occurs when excess solder forms a connection between two adjacent conductive features. This will result in a short circuit.
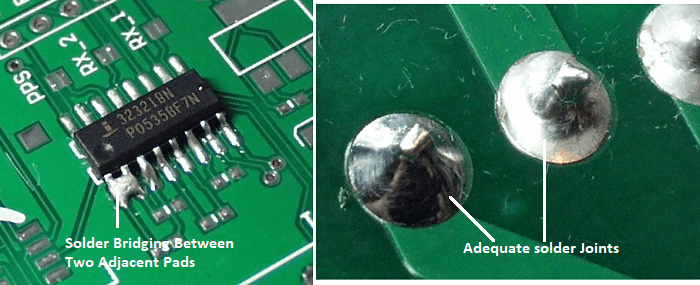
- Solder voids: Voids are gaps or bubbles in the solder joint that can reduce mechanical and electrical integrity.
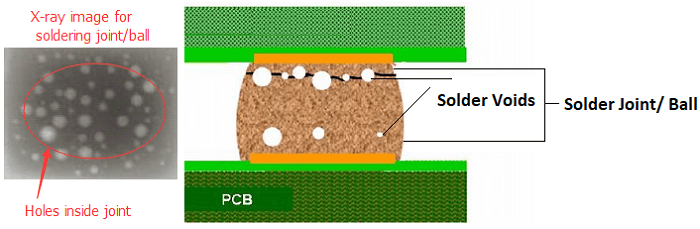
- Insufficient solder: Insufficient solder can result in a weak connection between the component and the PCB. This will lead to poor mechanical and electrical performance.
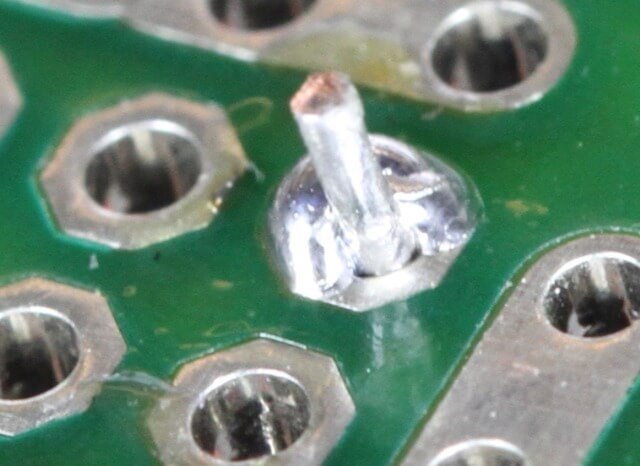
- Misaligned components: Components that are not correctly aligned during assembly can cause issues with connectivity, mechanical stability, and electrical performance.
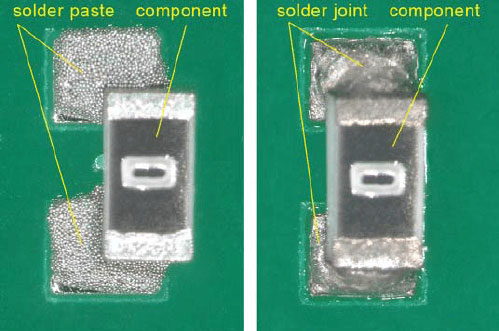
- Open circuits: An open circuit occurs when there is no electrical connection between two conductive features. This will result in a loss of functionality.
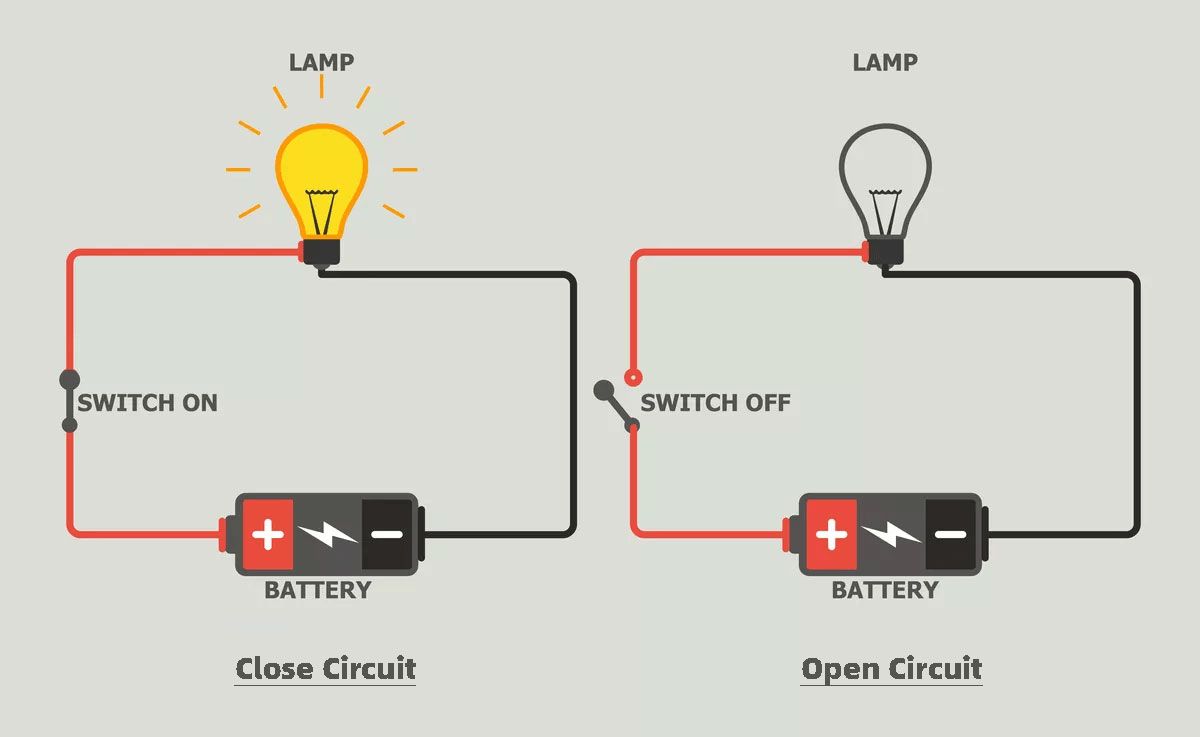
- Incorrect polarity: Components with a specific polarity, such as diodes and capacitors, must be correctly oriented during assembly; otherwise, they will not function as intended.
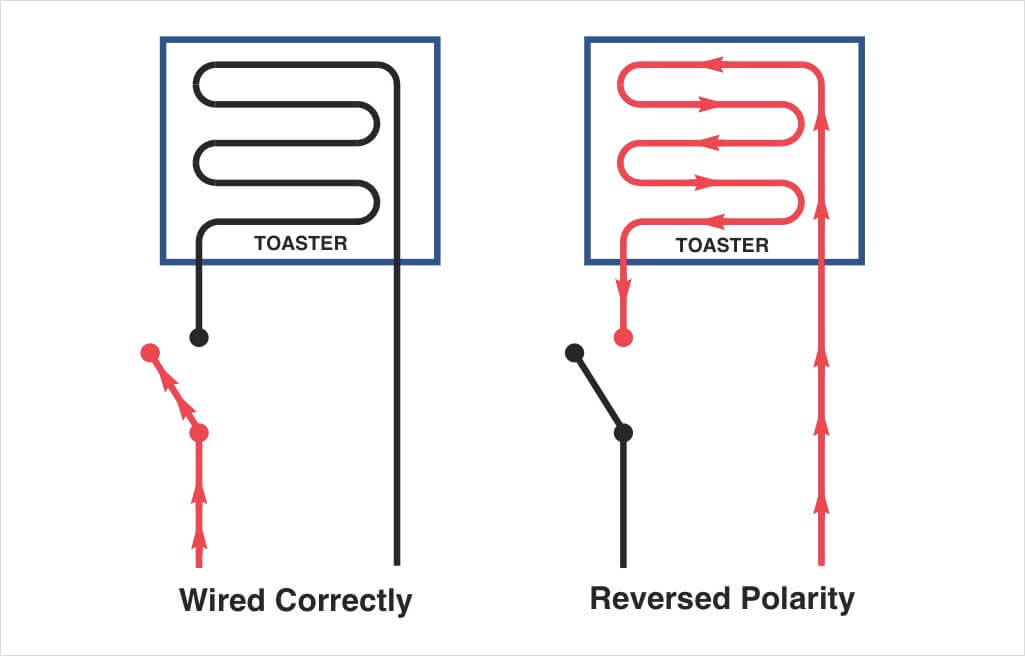
- Overheating: Overheating can occur during the soldering process, leading to component damage or even failure.
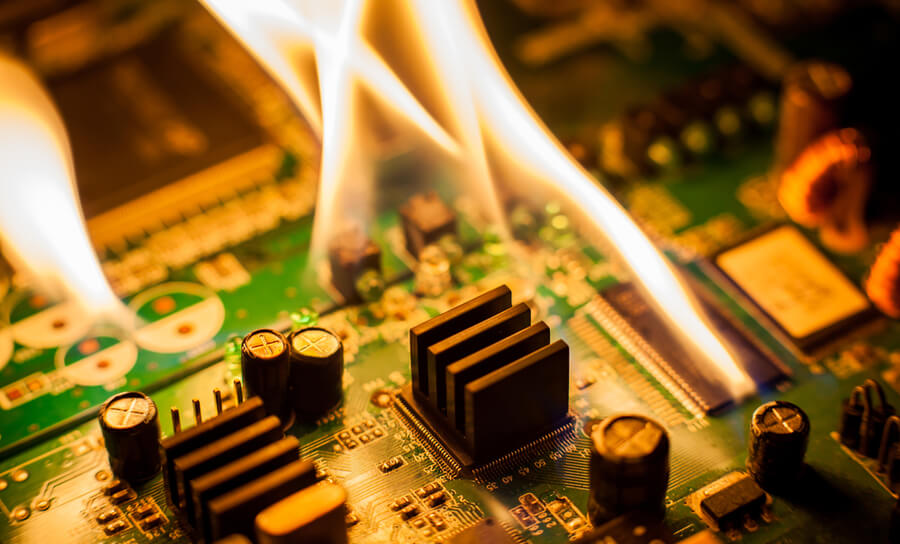
- Physical damage: Physical damage, such as scratches, cracks, or bent pins, can occur during handling, shipping, or assembly, affecting the mechanical and electrical integrity of the electronic assembly.
- Contamination: Contamination can occur during the assembly process and can lead to performance issues or failure of the electronic assembly.
IPC-A-600 Inspection Process
The IPC-A-600 standard outlines instructions for examining electronic assemblies to ensure they meet certain standards for quality and reliability. Usually, the examination process involves the following steps:
- Visual Inspection: To begin the inspection process, the electronic assembly will undergo a visual examination. The inspector's objective is to look for any signs of physical damage, contamination, or defects that could include misaligned components, solder bridges, and insufficient solder.
- Measurement and Testing: The inspector will use tools like calipers, gauges, and microscopes to measure and test conductor spacing, plating thickness, hole size, solder joint appearance, surface finish, and cleanliness of the electronic assembly.
- Classification: The electronic assembly will be categorized as either Class 1, Class 2, or Class 3 based on its intended usage and performance needs, following the inspection results.
- Acceptance Criteria: To determine if an electronic assembly is acceptable, the inspector will compare the inspection results with the acceptance criteria specified in the appropriate class of electronic assembly of the IPC-A-600 standard. The assembly needs to meet or surpass these criteria to be considered acceptable.
- Documentation: The documentation of the inspection process should include the inspection results, acceptance criteria, and all defects or issues discovered during the inspection.
Manufacturers can ensure top-quality and reliable electronic assemblies by adhering to guidelines and procedures. Consistent inspection and testing can detect problems early on, reducing the chances of larger issues arising later.
Training and Certification for IPC-A-600
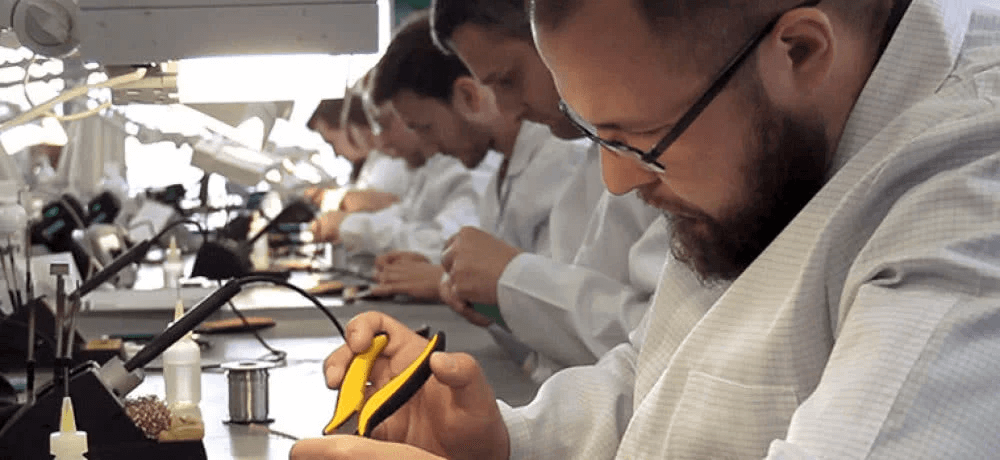
IPC-A-600 is a standard used in the electronic industry to provide guidelines for the quality and acceptability of electronic assemblies. IPC offers training and certification programs to individuals involved in the manufacturing, inspection, and testing of electronic assemblies to ensure that they meet the required standards. Here's an outline of the training and certification process for IPC-A-600:
- Training: IPC provides training courses that cater to individuals involved in the manufacturing, inspection, and testing of electronic assemblies. These courses cover the criteria and guidelines defined in IPC-A-600 and involve practical exercises and hands-on training.
- Certification: IPC has multiple certification programs related to IPC-A-600. These include the Certified IPC Specialist (CIS), Certified IPC Trainer (CIT), and Certified IPC Application Specialist (CIA). To become certified, individuals must take a written exam and undergo a hands-on skills assessment to demonstrate their comprehensive understanding of the standards and requirements outlined in IPC-A-600.
- Recertification: After two years, individuals with IPC certifications must complete a recertification program in order to keep their certification valid. Recertification programs usually consist of a review course and a written test.
Manufacturers can rely on IPC training and certification programs to equip their staff with the knowledge needed to produce electronic assemblies of unparalleled quality. This industry-leading program provides individuals involved in manufacturing, inspection, and testing a comprehensive understanding of best practices—as set forth by IPC-A-600 guidelines—to ensure that each assembly meets the highest standards without any performance or reliability issues.
Best Practices for Complying with IPC-A-600
To comply with IPC-A-600, manufacturers should follow these best practices:
- Develop a Quality Management System (QMS): To ensure that the product meets the desired quality standards, manufacturers must establish a QMS that comprises policies, processes, and procedures. This QMS must incorporate guidelines and criteria for electronic assemblies, such as IPC-A-600.
- Train employees: IPC-A-600 training should be provided to all employees who are involved in the manufacturing, inspection, and testing of electronic assemblies. The training should cover the guidelines and criteria specified in the standard, along with the best practices for adhering to these guidelines.
- Inspect assemblies regularly: Electronic assemblies need to be inspected on a regular basis by manufacturers in order to make sure that they meet the criteria specified in IPC-A-600 guidelines. The inspections should consist of visual checks as well as measurements and tests.
- Document inspections: The manufacturers must keep a record of all inspections conducted, which should contain details about the acceptance criteria, inspection outcomes, and any defects or issues identified.
- Address non-conformities: If the electronic assembly doesn't meet the standards in IPC-A-600, the manufacturer needs to make it right by fixing or replacing it. This could involve doing some rework or repairs.
- Use appropriate materials: To meet IPC-A-600 requirements, manufacturers must use the proper solder, adhesives, and coatings, and ensure proper storage and handling of materials.
- Maintain equipment: To ensure accurate results and proper functionality, manufacturers must perform regular maintenance and calibration on equipment used for manufacturing, inspecting, and testing electronic assemblies.
Manufacturers can guarantee their electronic assemblies conform to IPC-A-600 standards and produce top-notch products that fulfill customer expectations and don't have defects that might affect their performance or reliability by adhering to these best practices.
Conclusion
Adopting IPC-A-600 industry standards can help manufacturers produce reliable, high-quality electronic assemblies. Comprehensive inspection and testing processes, established training programs with certifications, and a well-developed Quality Management System that identifies and addresses any nonconformities encountered in production runs are all essential for meeting the requirements of this standard. Using materials designed specifically for electronics is also integral to protecting against defects or performance shortcomings. Furthermore investing in appropriate equipment helps maximize efficiency while maintaining product integrity — resulting in greater customer satisfaction and business success overall!