What is Aluminum PCB
Aluminum PCB is a type of printed circuit board and is also a type of metal core pcb. Among all metal core PCBs, aluminum PCBs are the most common type. Aluminum PCBs have two sides: one side is white and is used for soldering LED pins, while the other side exhibits the natural color of aluminum, typically coated with a thermally conductive paste to make contact with the thermal part. The base material consists of an aluminum core and an insulation layer, which provides thermal insulation and allows for efficient heat dissipation, thereby cooling the components and improving the overall performance of the product. Currently, aluminum PCBs are widely used in industries such as LED lighting and heat dissipation products.
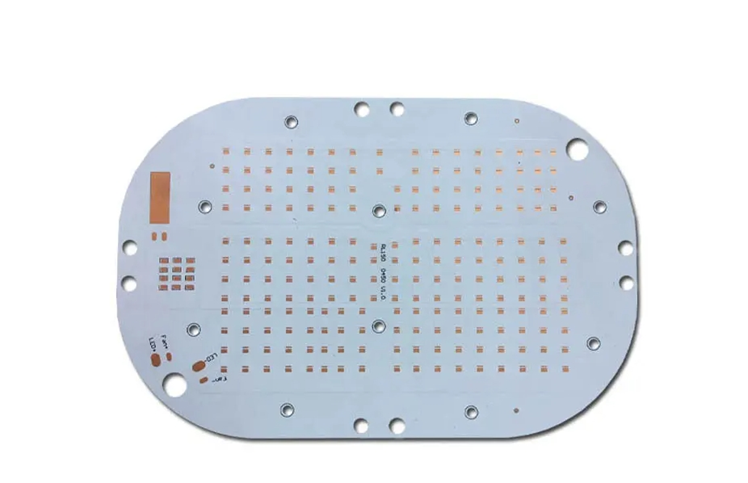
The Structure of Aluminum PCBs
The typical structure of an aluminum PCB is as follows:
- Top Layer: Copper Layer - This layer, located at the top of the aluminum PCB, is typically formed by depositing a layer of copper onto the aluminum PCB. The copper layer comprises conductive traces, wires, pads, etc., linking various components and devices.
- Middle Layer: Dielectric Layer - Positioned between the copper layer and the aluminum base layer, this layer exhibits excellent thermal conductivity. It provides electrical insulation and assist in effectively conducting and dissipating heat, thereby cooling electronic components and enhancing the overall performance of the product.
- Bottom Layer: Aluminum Base Layer - Situated at the bottom of the entire aluminum PCB, this layer is composed of aluminum base material. The aluminum base layer provides structural support and thermal conduction capabilities, aiding in the transfer of heat from electronic components to the surrounding environment, thereby helping to maintain the temperature of electronic devices within acceptable limits.
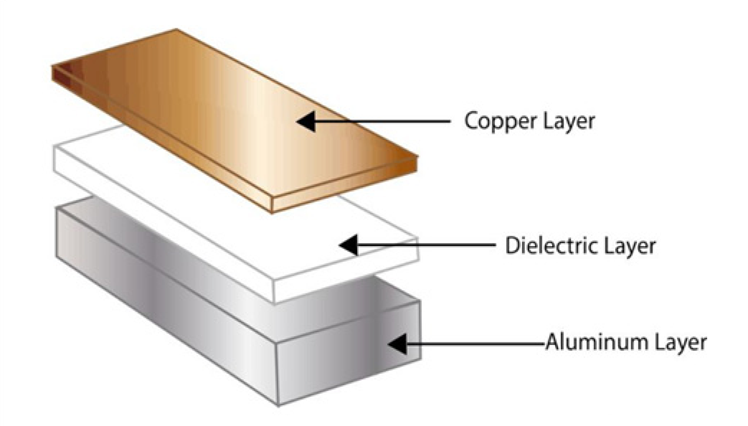
Single-Sided Surface Mount Aluminum PCB

The structure of a single-sided surface mount aluminum PCB is the simplest and easiest to manufacture, with the lowest cost. The routing is directly etched onto the copper layer of the aluminum substrate laminate. Heat transfers from the components to the routing layer, passes through the intermediate insulation thermal conductive layer, and then is transferred to the aluminum base layer.
Single-Sided Surface Mount Double-Layered Aluminum PCB
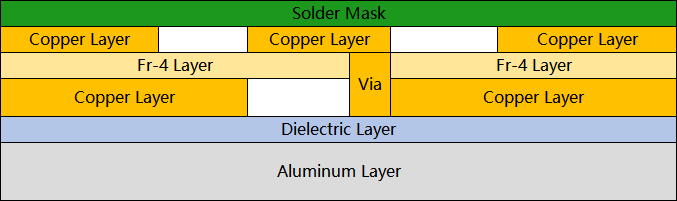
This type of PCB features two routing layers and insulation layers. Heat transfers from the components to the first routing layer, then to the first insulation layer, followed by the second routing layer, the second insulation layer, and finally to the aluminum layer.
Double-Sided Surface Mount Double-Layered Aluminum PCB
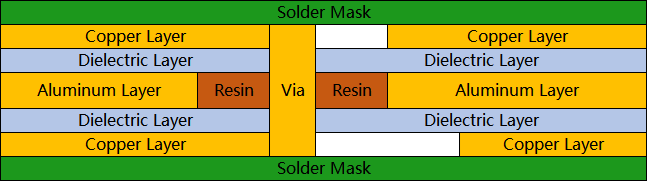
Sometimes, a single-sided component arrangement on an aluminum PCB may not meet the requirements, and the aluminum PCB can be designed for double-sided surface mounting. In this layered design, the top and bottom routing layers must pass through the aluminum base layer since aluminum is a good conductor, iInsulation treatment, such as filling insulation resin around the plated through-holes, is necessary. Heat generated by the components is transferred to the routing layer, then to the insulating layer, and finally to the intermediate aluminum base layer.
Advantages and Disadvantages of Aluminum PCBs
Aluminum PCBs offer several advantages, but they also have some disadvantages. Here are the main advantages and disadvantages of aluminum PCBs:
Advantages of Aluminum PCBs
- Environmental Friendliness: Aluminum is non-toxic and recyclable, meeting RoHS requirements. Its ease of assembly also contributes to energy-saving and sustainability for PCB suppliers.
- Excellent Heat Dissipation: High temperatures can severely damage electronic components. Aluminum demonstrates superior heat dissipation compared to standard FR-4 structures. The thermal conductivity of the dielectric material used is typically 5 to 10 times greater than that of conventional epoxy glass, with thicknesses typically one-tenth.
- Enhanced Durability: Aluminum offers strength and durability that ceramic or glass fiber substrates cannot match. Its robustness reduces the risk of accidental damage during manufacturing, transportation, and daily use.
- Lightweight: With lower density, aluminum PCBs enable sleeker and lighter designs. In weight-sensitive fields like aerospace and mobile devices, aluminum PCBs provide superior performance and reliability.
Disadvantages of Aluminum PCBs
- Higher Cost: Aluminum PCBs typically have a higher cost compared to conventional fiberglass-based PCBs. This is due to the relatively complex manufacturing process and the use of higher-cost materials.
- Higher Process Complexity: Welding and routing on aluminum PCBs are relatively complex and require special techniques and processes, increasing production difficulty and cost.
- Limited to Specific Applications: Due to their excellent heat dissipation capabilities, aluminum PCBs are particularly suitable for applications with high-power electronic devices that have high heat dissipation requirements. They may not be the best choice for low-power or low-heat applications.
- Overall, while aluminum PCBs offer advantages such as environmental friendliness, excellent heat dissipation, durability, and lightweight design, they also come with higher costs and process complexities. Their suitability depends on the specific application requirements and the trade-offs between heat dissipation and other factors.
Applications of Aluminum PCBs
Aluminum PCBs have a wide range of applications and can be found in various industries such as audio equipment, power devices, communication electronics, office automation equipment, automotive, computers, and power modules.
- Audio Equipment: Input/output amplifiers, balanced amplifiers, audio amplifiers, preamplifiers, power amplifiers, etc.
- Power Supply: Switching regulators, DC/AC converters, SW adjusters, etc.
- Communication Electronics: High-frequency amplifiers, filtering devices, transceiver circuits, etc.
- Office Automation Equipment: Motor drivers, etc.
- Automotive: Electronic regulators, ignition systems, power controllers, etc.
- Computers: CPU boards, floppy disk drives, power devices, etc.
- Power Modules: Inverters, solid-state relays, rectifier bridges, etc.
These are just a few examples, and the versatility of aluminum PCBs allows them to be utilized in many other applications where heat dissipation, durability, and reliability are essential.
Manufacturing Challenges of Aluminum PCBs
The performance, quality, processability, manufacturing standards, manufacturing costs, long-term reliability, and stability of aluminum PCBs largely depend on the aluminum-clad copper laminate. Aluminum PCBs offer excellent electrical performance, heat dissipation, electromagnetic shielding, high dielectric strength, and bendability. As a metal core PCB, whether it is a single-sided, double-sided, or multi-layer aluminum PCB, they share many similarities in manufacturing techniques with FR4 PCBs, such as etching thick copper foils, aluminum surface etch protection, aluminum board fabrication, and solder mask printing. However, as an advanced type of PCB, aluminum PCBs still have specific aspects in the manufacturing process that require strict and effective management and control. Then, let’s take a look at what factors need to be considered and manufacturing challenges when producing aluminum PCBs.
- Mechanical Processing: When drilling aluminum substrates, no burrs are allowed on the edges of the back hole and the inner hole, which will affect the pressure testing. Milling the shape is extremely challenging. Forming the shape through punching requires the use of advanced molds, the production of which demands skill and is one of the difficulties in aluminum substrate manufacturing. After forming the shape, the edges must be very neat, free from any burrs, and must not damage the solder mask on the board edges. Typically, punch dies are used, with holes punched from the circuit traces and shapes punched from the aluminum surface. Techniques such as force application during circuit board punching (up-cut and down-pull) require skill. After forming the shape, the curvature of the board should be less than 0.5%.
- Avoiding Scratches on Aluminum Surfaces: Any contact with the aluminum surface by hand or exposure to certain chemical substances can cause discoloration or blackening, which is absolutely unacceptable. Some customers even refuse to accept re-polished aluminum surfaces. Therefore, avoiding scratches or contact with the aluminum surface throughout the entire process is one of the challenges in producing aluminum-based circuit boards. Some companies use passivation processes, while others apply protective films before and after hot air leveling (HASL), employing various techniques to achieve this goal.
- High Voltage Testing: Communication power aluminum substrates require 100% high voltage testing. Some customers specify direct current (DC), while others require alternating current (AC), with voltage requirements ranging from 1500V to 1600V and testing durations of 5 to 10 seconds, respectively, for 100% of the printed boards. Any contaminants on the board surface, burrs around holes and aluminum edges, sawtooth patterns on traces, or even slight damage to the insulation layer can lead to ignition, leakage, or breakdown during high voltage testing. Boards with delamination or bubbling after high voltage testing are rejected.
- Thick Copper Etching: Aluminum PCBs are typically used in power equipment with high power density, hence the copper foil tends to be thicker. When the copper foil thickness is 3oz or higher, etching the copper foil requires compensation for trace width. Otherwise, the traced width after etching will exceed the tolerance range. Therefore, to ensure optimal trace width/spacing and impedance control to meet design requirements, it is necessary to design appropriate trace width compensation in advance, eliminate the influence of trace manufacturing on trace width/spacing, and strictly control etching factors and reagent parameters.
- Solder Mask Printing: Solder mask printing is considered a manufacturing challenge in aluminum PCBs due to the presence of thick copper foils. If the copper thickness on the traces is too large after image etching, there will be a significant difference between the trace surface and the substrate, making solder mask adhesion difficult. To ensure successful solder mask printing, high-quality performance solder resist should be used, and double printing of the solder mask may be necessary. In some cases, resin filling followed by solder mask printing may be employed.
- Mechanical Manufacturing: Mechanical manufacturing of aluminum PCBs includes mechanical drilling, milling and shaping, as well as V-cutting. Burrs are often left in the internal vias during drilling, which can reduce electrical strength. Therefore, to ensure high-quality mechanical manufacturing, especially in small batch production, electric milling cutters and specialized milling cutters should be selected. Attention should be paid to controlling technology and patterns during molding. Drill parameters should be adjusted appropriately on thick copper aluminum PCBs to prevent burrs during production.
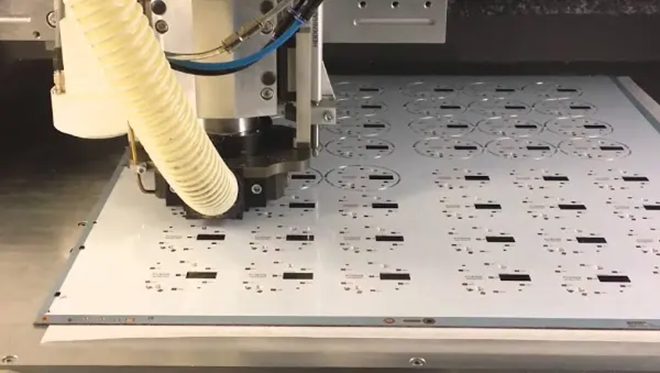
View our manufacturing capacity of Aluminum PCB in the table below:
NEXTPCB Manufacturing Capacity of Aluminum PCB
Items
|
Manufacturing Capabilities
|
Material
|
Aluminum core (Domestic 1060), Copper core, FR4 covering
|
Thermal conductivity
|
1.0W/(m*k),2.0W/(m*k)
|
Min. Track/Spacing
|
4mil
|
Min. Hole Size
|
0.8mm
|
Base Material
|
Aluminum, FR4, Flex, Flex-rigid, HDI, Rogers, etc.
|
Board Thickness
|
0.4-3.2mm
|
Surface Finishing
|
Immersion gold, OSP, Hard Gold, Immersion Silver, ENEPIG
|
Finish Copper Weight
|
1-4oz
|
Solder Mask
|
Green, Red, Yellow, Blue, White, Black, Purple, Matte Black, Matte green
|
Silkscreen
|
White, Black
|
Via Process
|
Tenting Vias, Plugged Vias, Vias not covered
|
Testing
|
Fly Probe Testing (Free) and A.O.I. testing
|
Aluminum PCB Quote Online
If you have heat dissipation issues in your PCB design, aluminum PCB should be your First Choice. NextPCB provides all types of aluminum PCB, including single-sided aluminum PCB, multilayer aluminum PCB, mixed aluminum PCB, flexible aluminum PCB, through-hole aluminum PCB, and Other categories, such as general-purpose aluminum PCB, high thermal conductivity aluminum PCB, and high-frequency aluminum PCB, etc. If you need more detailed information about our aluminum PCB, please contact us(email to support@nextpcb.com).